Indoor Localization of Mobile Vehicles for Intelligent Manufacturing Task Planning Based on Game Machines
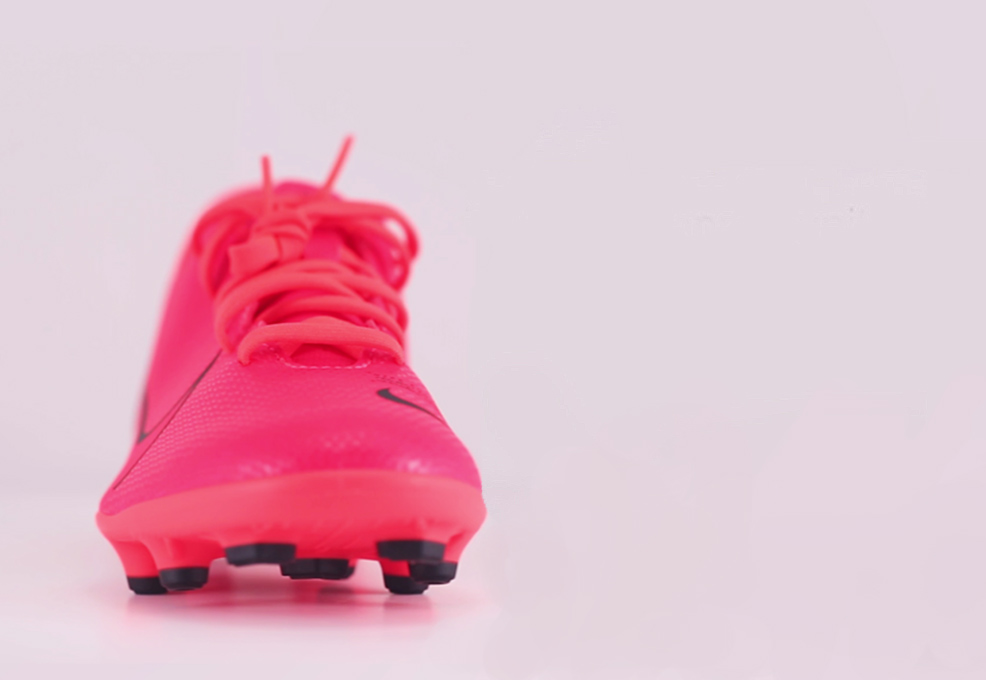
Author(s)
Jin H. HuangBiography
Professor Jin H. Huang received his Ph.D. degree from the Department of Mechanical Engineering of Northwestern University, USA. He joined Feng Chia University in 1993. He was the Dean of Mechanical Engineering, the founder and director of the Master Program of Electro-Acoustics, the Dean of the College of Engineering and the Director of the Office of Industry-Academia Cooperation. He received the honor of lifetime distinguished professor in 2015. Prof. Huang is active in the technology development committee of the MOST, including the governmental technology development project review committee, the defense technology academic cooperation review committee, the research project review committee, and high-tech equipment technology development project review of the central science park. He is currently the Vice President of Feng Chia University. Prof. Huang is an expert in parametrical optimization and structural acoustics. He received the excellence in research award and grant in 2015 and the excellence in university-industry technology alliance award from the MOST. His research interests are vibration and noise control, thermal and vibration analysis of high-speed spindle under the running state. He has a strong connection with international industries and academia.
Academy/University/Organization
Feng Chia University-
TAGS
-
Share this article
You are free to share this article under the Attribution 4.0 International license
- ENGINEERING & TECHNOLOGIES
- Text & Image
- August 20,2020
Facing the trend of High-Mix Low-Volume production, most Taiwanese manufacturing companies are considering digital transformation to increase their capability to face the challenge of future production. The steady governmental support for the development of artificial intelligence has established a strong platform for public and private partnerships (PPP) to form a strong link between hardware/software development and university/institute/enterprise (including the end-user) partnerships, to accelerate the digital transformation. The project “Developing a Smart Automation Mechatronics System and Internet of Things for Shoe Manufacturing” led by Professor Jin-Huang Huang, the vice president of Feng Chia Univerity, is developing the key operation and information technologies to help the digital transformation of traditional shoe manufacturing companies. Various automation designs with innovative mechanisms and the integration of robots, vision inspection and conventional sewing machines have been implemented to replace labor-intensive work. A 30% manufacturing efficiency improvement can be expected. A low-cost vibration sensor with partial edge-computation power is wirelessly connected to a cloud-based database server to continuously capture the machine utilization rate. Daily production efficiency reports can be generated to allow the factory managers to sustainably execute Kaizen engineering. A 20% increase in production can be achieved based on the field implementation.The success of the project is not only a technology breakthrough but also promotes the new idea of the digital transformation platform. A win-win-win situation can be further achieved by the successful digital transformation of the manufacturing companies, the business growth of the solution providers, and the industrial experience and applied research of the academy.
For decades, Taiwan’s traditional manufacturing companies have supported economic growth through continuous business and technology innovations. Most companies have built a strong global network with acknowledgment of the technology developments to be flexible to the fast market change, for instance, the trend of High-Mix Low-Volume production. Besides the professional production technologies, most Taiwanese manufacturing companies, like others all over the world, are considering digital transformation to increase their capability to face the challenge of future production.
Fortunately, there are two major advantages for Taiwanese manufacturers to conduct digital transformation. First, the worldwide leading IT hardware design house and manufacturers, such as TSMC, Acer, and NVIDIA, are Taiwanese companies. Secondly, the steady support of artificial intelligence development from the government has established a strong platform for public and private partnerships (PPP) to form a strong link between the hardware/software development and university/institute/enterprise (including the end-user) partnerships to accelerate digital transformation.
For example, the project “Developing a Smart Automation Mechatronics System and Internet of Things for Shoe Manufacturing” (MOST-107-2218-E-035-016), led by Professor Jin-Huang Huang, the Vice President of Feng Chia Univerity, received three-year funding from the Ministry of Science and Technology. This project is developing the key operation and information technologies to help the digital transformation of traditional shoe manufacturing companies. There are nine different industries involved, including three technology providers and six end-users (shoe manufacturers). Moreover, 13 multidisciplinary professors from four different universities with 38 graduated researchers are working day-and-night to develop the platform technologies, which are able to be customized based on the industry-specific requirements.
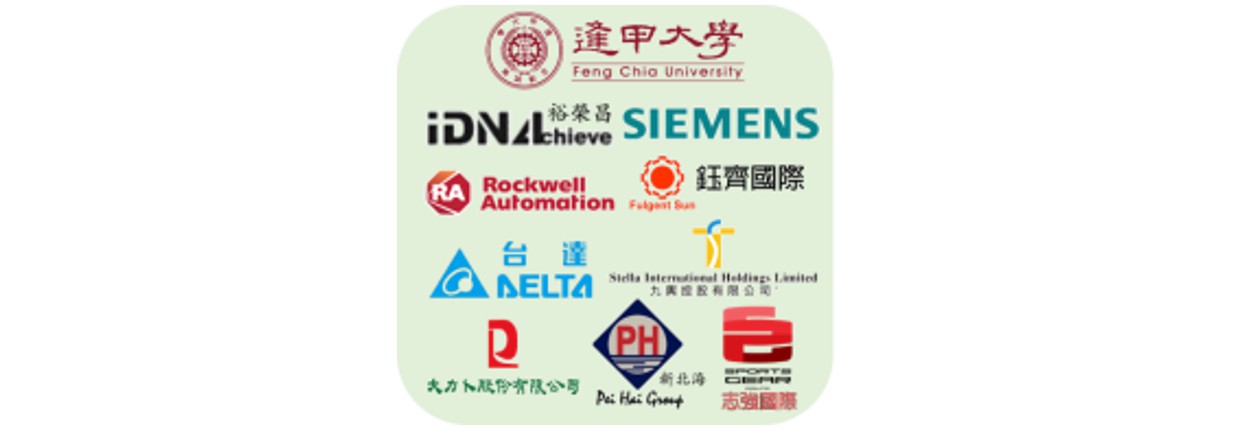
Various automation designs with innovative mechanisms and the integration of robots, vision inspection and conventional sewing machines have been implemented to replace labor-intensive work. A 30% manufacturing efficiency improvement can be expected. These designs have been accomplished by co-operation between the university and industry, following the Conceive, Design, Implement and Operate (CDIO) procedure. Moreover, this project is also developing advanced factory modeling with push and pull production and scheduling algorithms to enable prediction capability and the implementation of the lean manufacturing concept. Furthermore, specific internet of things (IoT) hardware and software have been developed, especially for the reality of the shoe manufacturing site. A low-cost vibration sensor with partial edge-computation power is wirelessly connected to a cloud-based database server to continuously capture the machine utilization rate. Daily production efficiency reports can be generated to allow the factory managers to sustainably execute Kaizen engineering. A 20% increase in production can be achieved based on the field implementation. More than that, the machine learning technologies have been applied to analyze the IoT data, in order to develop the smart factory decision algorithm. The neural network model can predict the output of the whole-day labor-intensive continuous production line within a 5% error, based on less than 30 minutes of IoT data.
The success of the project is not only a technology breakthrough ,but is also promoting the new idea of the digital transformation platform. Under the guidance of the MOST, Feng Chia University is developing the digital transformation platform to serve traditional manufacturing companies. More than academic research, new technologies, such as augmented reality, AI with smart factory analysis and a dashboard system, heterogeneous integration from the newborn companies, and world-leading solution providers are actively involved and are evolving together with the academy. For a particular manufacturing company, the initial digital transformation solution can be generated from this platform and then grown by the professional solution providers. A win-win-win situation can be achieved by the successful digital transformation of the manufacturing companies, the business growth of the solution providers, and the industrial experience and applied research of the academy.
STAY CONNECTED. SUBSCRIBE TO OUR NEWSLETTER.
Add your information below to receive daily updates.