The Sharing of a Wireless Power Charging Facility to Create a Smart Future
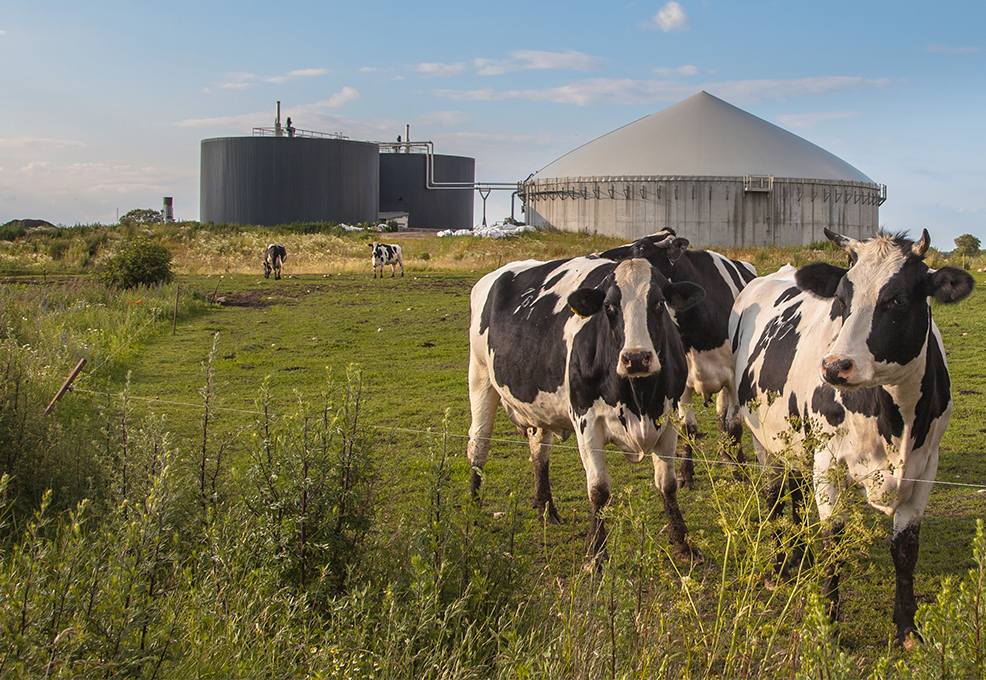
Author(s)
Chen-Yeon Chu & Chiu-Yue LinBiography
Prof. Chu is currently an associate professor in the Master’s Program of Green Energy Science and Technology. Prof. Lin is a chair professor in the Department of Environmental Engineering and Science at Feng Chia University (FCU). They work on biohythane gaseous fuel production using anaerobic fermentation technology from bio-waste.
Academy/University/Organization
Feng Chia UniversitySource
https://doi.org/10.1016/j.biortech.2019.122702
http://ap.fftc.agnet.org/ap_db.php?id=1029-
TAGS
-
Share this article
You are free to share this article under the Attribution 4.0 International license
- ENGINEERING & TECHNOLOGIES
- Text & Image
- August 20,2020
Hythane, defined as a gas mixture of hydrogen (H2) and methane (CH4), has been an attractive alternative vehicle fuel since the 1980s. Most of the hythane production processes in practice add H2 into CH4 but have the disadvantage of using fossil-fuel-dependent H2. Thus, since the 2000s, many studies have focused on a more sustainable process called two-stage anaerobic biohythane production (HyMeTek), in which biohydrogen and biomethane are separately generated in two digesters and then mixed together to obtain biohythane. The overall energy recovery remarkably increases (8-43%) for the two stages in the huge majority of experimental conditions, and never decreases. These initial results may drive further research to better understand the conditions that can promote the two-stage anaerobic digestion to higher performance. The two-stage biohythane pilot plant was also used to assist Indonesian refugees who were affected by climate change, providing local farmers and refugees with sustainable energy, and solving the pollution caused by agricultural waste. The biohydrogen research team at Feng Chia University used biowaste as a feedstock and built the world’s first two-stage biohydrogen and biomethane power plant on XinHeXing pig farm, Nantou, Taiwan, to resolve the dilemma of food supply and waste treatment, lighting up the world by “turning the brown into the new green.”
Dark fermentation is the most promising technology to produce bioenergy from organic materials. The two-stage H2/CH4 fermentation process was developed during the last decades. To efficiently convert biomass wastes and wastewaters into bioenergy, pretreatment is necessary via adjusting feedstock conditions (e.g., pH, temperature and carbon/nitrogen ratio) before applying the two-stage fermentation process. For lignocellulosic materials, breaking the lignin seal, feedstock size/structure and modifying the chemical composition of the biomass are important. The pretreatment process can be classified into biological, physical, chemical and physic-chemical methods. A combination of these methods has also been performed. Furthermore, a separator unit such as the activated sludge method might be applied to remove effluent chemical oxygen demand (COD) to meet the discharge standard. Feng Chia University’s biohydrogen research team has successfully developed high-rate biohydrogen production anaerobic technologies with granular mixed microflora (Fig. 1). The more bacteria there are, the better the hydrogen production. However, microbes are as tiny as particulates. They are easily washed out of the reactor. Therefore, creating immobilized granules to keep microorganism in the bioreactor is the most important technology for biohydrogen production. How would the bacteria survive if they are wrapped in granules? A granule is like a house. Bacteria can live there and reproduce. They would not die. Microbes have sporulated and are mixed with activated carbon during the drying process, then mixed with sodium alginate to form granules. With enough nutrients, microbes can rapidly reproduce. Microbes will form more microbial granules. The bigger and the more granules there are, the better the hydrogen production. The biohydrogen was produced at the rate of 15 liters per hour per liter of reactor volume by the biohydrogen research team at Feng Chia University. This value is the best in biohydrogen production in the world so far.
Fig. 1. High-rate biohydrogen production with granular mixed microflora.
There are advanced bioreactors of continuously-stirred anaerobic bioreactors (CSABR), carrier induced granular sludge beds (CIGSB) and agitated granular sludge bed reactors (AGSBR) being operated at particularly short hydraulic retention times (0.5-1.5 h) and attaining high biomass concentrations. These reactors reached high hydrogen production rates (HPR) due to the fact that higher biomass concentrations are contact-effective between granular microflora and substrates. Some pilot-scale studies from synthetic and raw wastewaters have been reported. Novel two-stage hydrogen and methane production technology and its operation technology have been established and named as “Innovative Hydrogenation & Methanation Technology (HyMeTek).” To commercialize this HyMeTek technology, a verification scale of the HyMeTek system including a hydrogen production fermenter (60 m3) and a methane fermenter (600 m3) were built on the XinHeXing pig farm, Nantou, Taiwan (Fig. 2).
Fig. 2. Commercial HyMeTek system on a pig farm located in Nantou, Taiwan.
Fig. 3 shows the Symnergy (symbiosys bioenergy) conceptual model for a self-sustaining community. The Symnergy model is an integrated model of biowaste management to produce several benefits for environmental and social impacts on the community such as in the economy, education and job creation. The output of the Symergy model is biogas, bioelectricity and biofertilizer, and the model supports the community to be self-sustaining in the fields of bioenergy, bioeconomy and agriculture. Bailang village was chosen to embed the HyMeTek pilot module as a demo site for verification of the “symnergy model for a self-sustaining community.” There are a number of flood victims' families in Bailang village, and the location was adjacent to the slaughterhouse as a biowaste source for biogas. There was a lack of access to electric power in certain houses. Many low-income dwellers live in this area. The lower income led them to have lower education and lack of job opportunities leading to lower economic standards. If the pilot module project is successful, it will be easy to develop such systems in other villages. It was found that the people have positive awareness and acceptance of the social and environmental impacts after the HyMeTek pilot module was built. It can create 2.5 jobs and provide 280 visitors per year. The 25-30 head of cattle in the cowshed can produce 10-30 kg/day of biowaste and 2 m3/day of wastewater as a substrate for biogas production in the pilot module. The biogas of 1.3 m3/day was collected to replace the LPG, and saved approximately USD90.78/year. The villagers can gain extra income of around USD130.08/year from bioelectricity production. In addition, the village can earn around USD400-500/year by selling chilies which use biofertilizer produced from the pilot module. Finally, the environmental and community impact of the Symnergy model which imported the HyMeTek pilot module were successful as verified in the self-sustaining community.
Fig. 3. Symnergy model for a self-sustaining community by importing the HyMeTek pilot plant in Manado City, Indonesia.
STAY CONNECTED. SUBSCRIBE TO OUR NEWSLETTER.
Add your information below to receive daily updates.